Stunning Info About What Is PLC In Electrical Panel
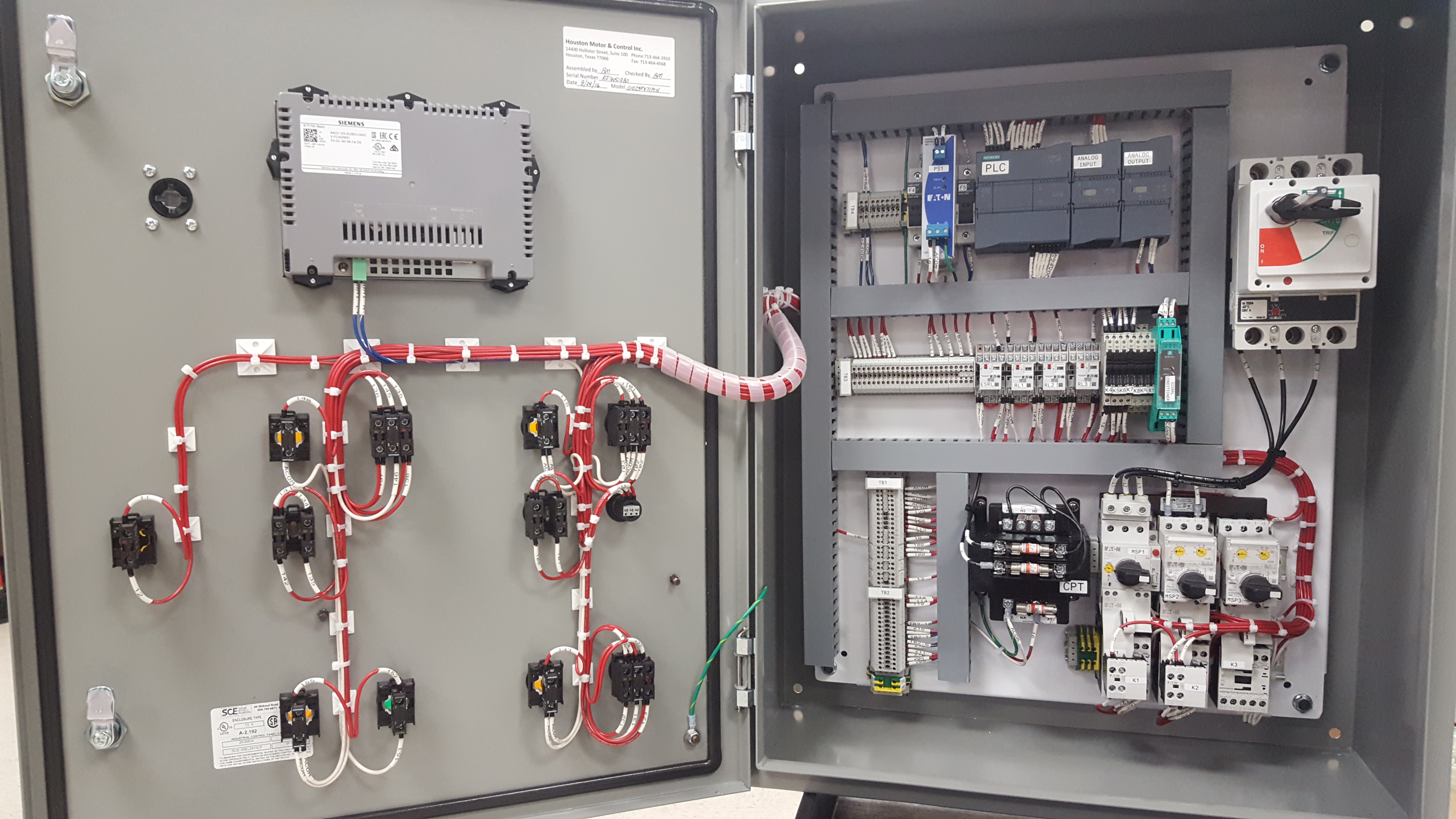
Plc Control Panel Design
Unlocking the Mystery of PLCs in Electrical Panels
1. What's the Deal with PLCs Anyway?
Ever stared into an electrical panel and wondered what all those little boxes and wires are doing? Well, nestled in that organized chaos, you might find something called a PLC. PLC stands for Programmable Logic Controller, and trust me, it's way cooler than it sounds. Think of it as the brains of the operation — a miniature computer specifically designed to control machines and processes.
Instead of hardwiring everything with relays and timers, which can get incredibly messy and difficult to change, PLCs use software. This means you can modify the control logic just by changing the program, making them incredibly flexible and efficient. Imagine trying to rewire a whole factory floor every time you wanted to change something! With a PLC, it's a matter of a few keystrokes.
So, why are PLCs so important in electrical panels? Simply put, they bring intelligence and automation to the party. They can monitor sensors, control motors, operate valves, and make decisions based on pre-programmed instructions. They're the workhorses of modern industry, ensuring everything runs smoothly and efficiently.
And because they're programmable, PLCs can handle complex control scenarios that would be nearly impossible with traditional hardwired systems. Plus, they're often networked together, allowing for centralized monitoring and control of entire systems. Pretty neat, huh?
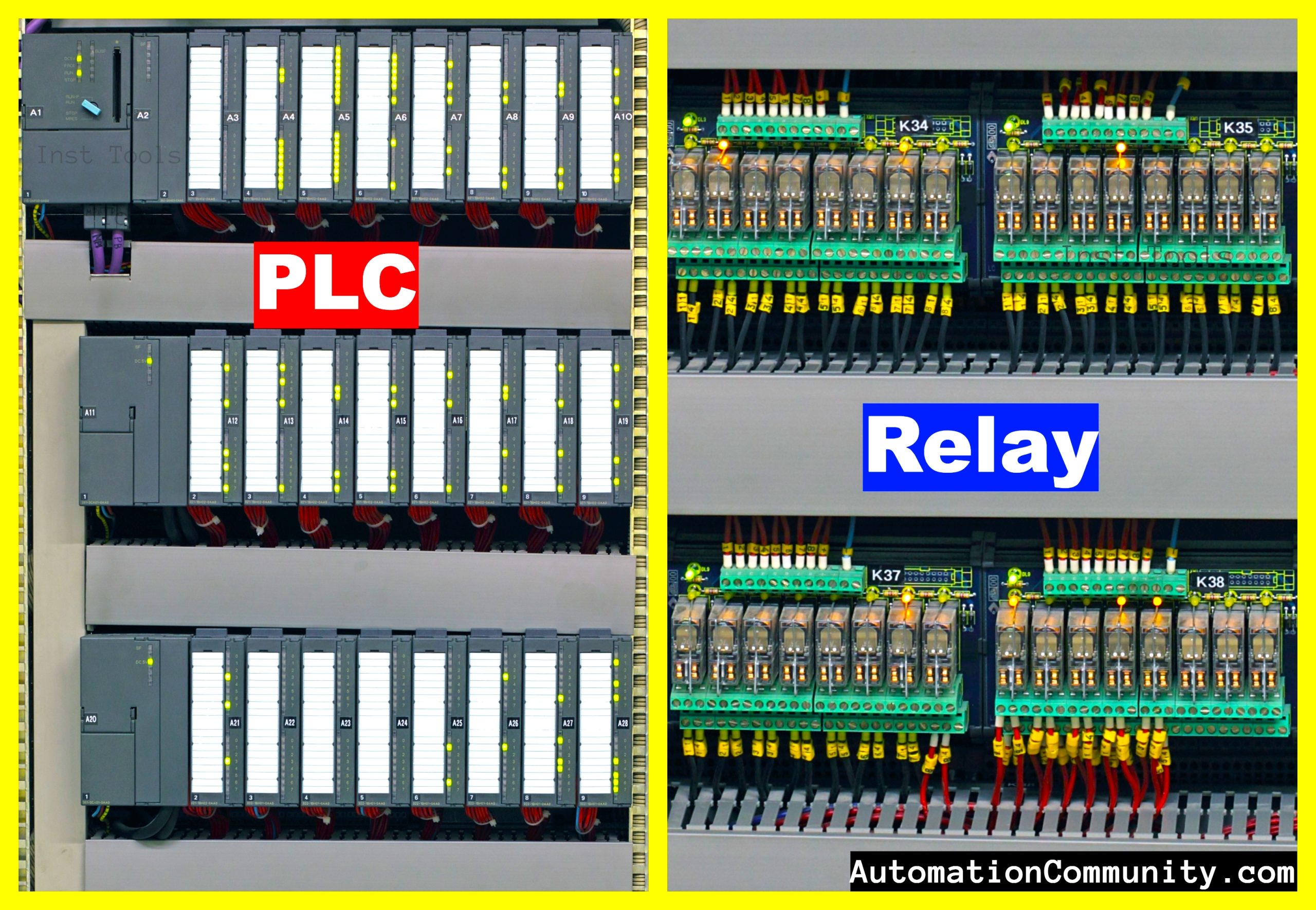
Difference Between Safety Plc And Normal At Marco Lloyd Blog
Why Are PLCs So Common in Electrical Panels?
2. The PLC Advantage
Okay, so we know PLCs are programmable and control things. But what makes them so ubiquitous in electrical panels, practically the rockstars of industrial automation? It boils down to a few key advantages. First, there's the versatility. Need to change the way a machine operates? No problem, just tweak the PLC program. It's like having a remote control for your entire industrial process.
Then there's the reliability factor. PLCs are designed to withstand the harsh environments of industrial settings — think extreme temperatures, vibration, and electrical noise. They're built tough, which means less downtime and more productivity. Nobody wants a control system that crashes every time a machine sneezes.
Another big advantage is diagnostics. PLCs can provide detailed information about the status of the system, making it easier to troubleshoot problems. Instead of blindly poking around with a multimeter, you can use the PLC's diagnostic tools to pinpoint the exact cause of a fault. Talk about a time-saver!
Plus, PLCs offer advanced features like data logging, communication with other devices, and even web-based monitoring. This means you can keep tabs on your system from anywhere in the world. Imagine sipping coffee on a beach while monitoring your factory floor from your laptop. Okay, maybe that's a bit of a stretch, but the possibilities are there!
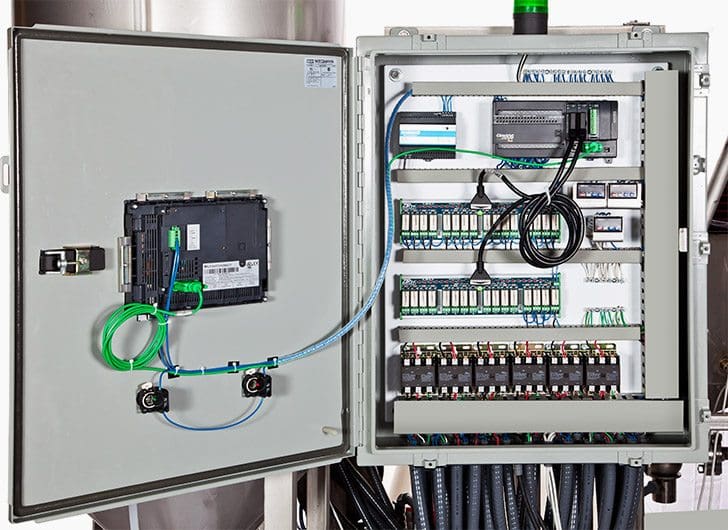
Wiring Diagram Of Electrical Panel Digital And Schematic
Breaking Down the PLC Components Inside the Panel
3. What Makes a PLC Tick?
So, what exactly is inside that unassuming box we call a PLC? Well, it's not just a magical black box (though sometimes it feels like it). A typical PLC system consists of several key components that work together to make the magic happen. First, there's the CPU, or Central Processing Unit. This is the brains of the PLC, where the program is executed and decisions are made. It's like the conductor of an orchestra, orchestrating the entire control process.
Next, we have the input modules. These are the PLC's senses, allowing it to receive information from the outside world. They connect to sensors, switches, and other devices that provide data about the process being controlled. Think of them as the eyes and ears of the PLC.
Then there are the output modules. These are the PLC's muscles, allowing it to control external devices. They connect to actuators, motors, valves, and other devices that perform actions based on the PLC's decisions. They're the hands and feet of the PLC, carrying out its instructions.
Finally, there's the power supply, which provides the necessary electricity to keep everything running. And of course, there's the programming interface, which allows you to write and upload programs to the PLC. It's the PLC's voice, allowing you to tell it what to do.
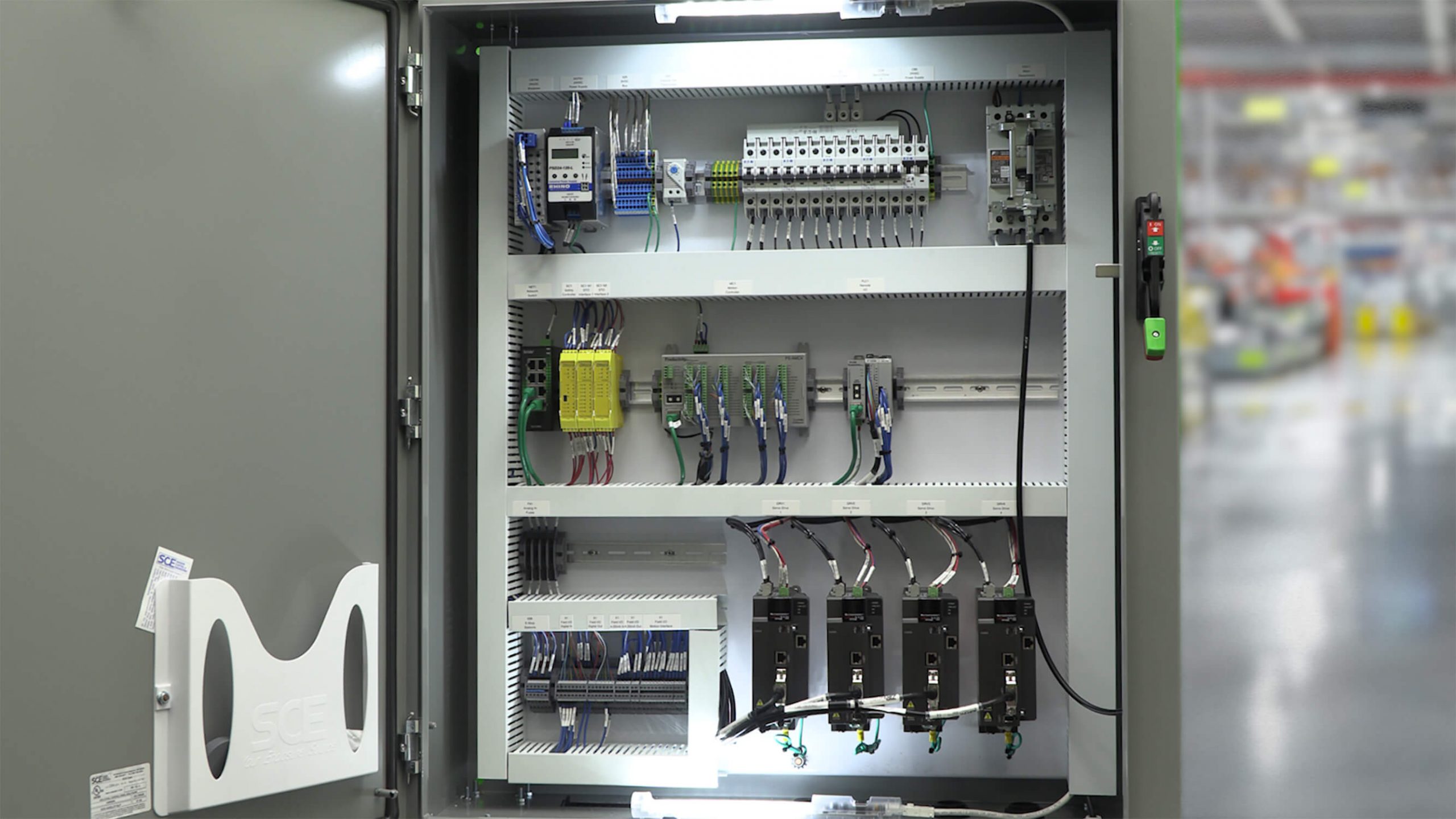
Troubleshooting PLCs
4. Don't Panic! A Basic Troubleshooting Guide
Let's face it: even the most reliable PLCs can sometimes throw a tantrum. When things go wrong, it's important to have a basic understanding of troubleshooting techniques. First and foremost, check the obvious things. Is the PLC powered on? Are all the connections secure? Sometimes the simplest solution is the correct one. Always start with the easy stuff!
Next, use the PLC's diagnostic tools to check for error messages. These messages can often provide clues about the cause of the problem. Consult the PLC's documentation to understand what the error messages mean. It's like reading the PLC's diary — full of hints and secrets.
If you suspect a problem with a sensor or actuator, use a multimeter to check its voltage and current. Make sure the device is receiving the correct signals. Sometimes a faulty sensor can send the PLC into a tailspin.
And if all else fails, don't be afraid to consult with a qualified PLC technician. They have the experience and expertise to diagnose and repair even the most complex problems. Remember, sometimes it's better to call in the pros.
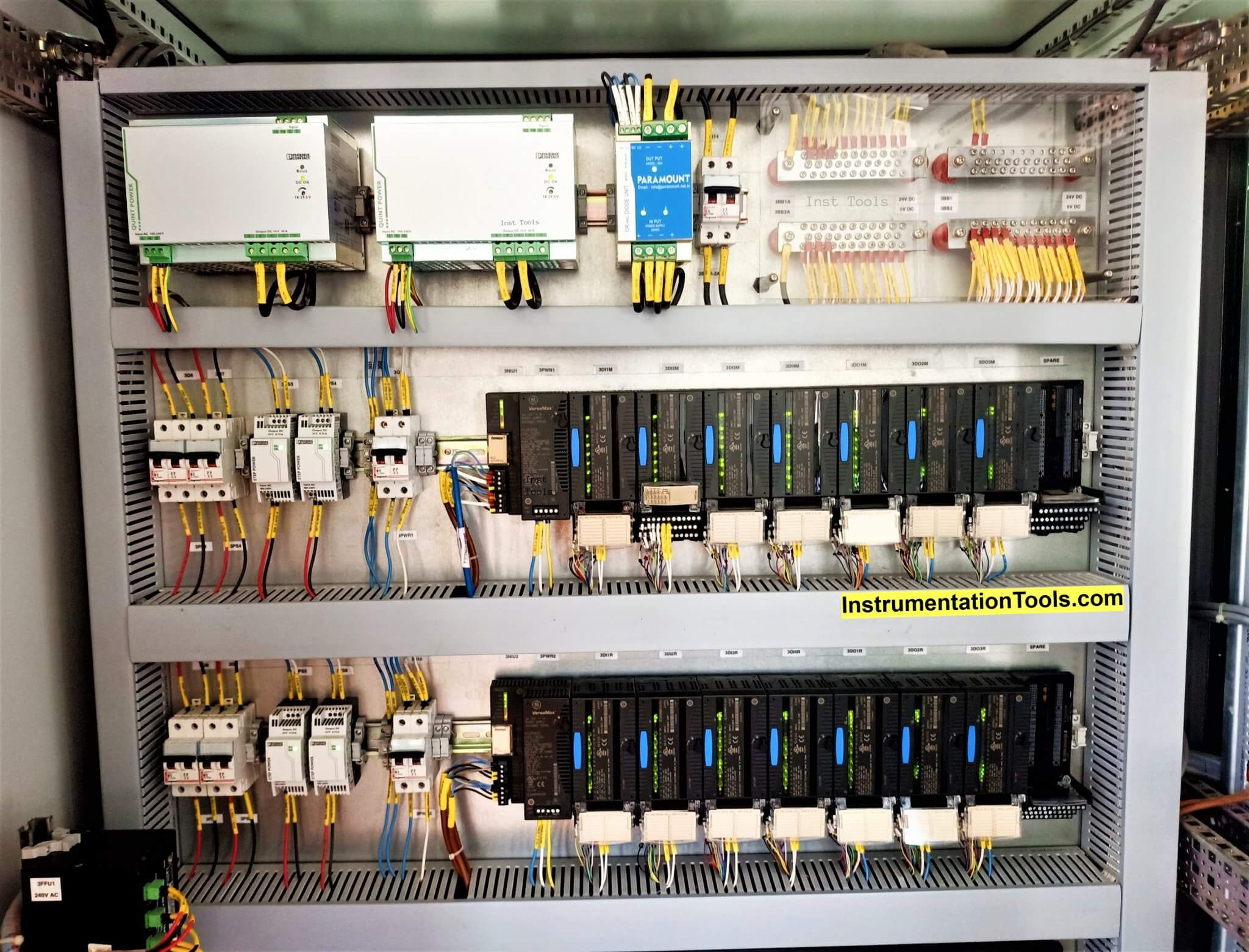
Wiring In A PLC Control Panel Basic Electrical Design
The Future of PLCs
5. PLCs Evolving in the Modern World
The world of industrial automation is constantly evolving, and PLCs are evolving right along with it. One of the biggest trends is the increasing use of Ethernet-based communication. This allows PLCs to connect to networks, share data with other devices, and be monitored remotely. It's like giving the PLC a smartphone and a social media account.
Another trend is the integration of PLCs with cloud-based platforms. This allows for centralized data storage, analysis, and visualization. Imagine being able to track the performance of all your PLCs from a single dashboard. It's the ultimate in industrial intelligence.
We're also seeing the rise of more powerful and flexible PLCs that can handle complex control tasks with ease. These PLCs often incorporate advanced features like machine learning and artificial intelligence. It's like giving the PLC a brain upgrade.
So, what does the future hold for PLCs? More connectivity, more intelligence, and more automation. PLCs will continue to play a vital role in industrial automation, helping businesses improve efficiency, reduce costs, and stay competitive.
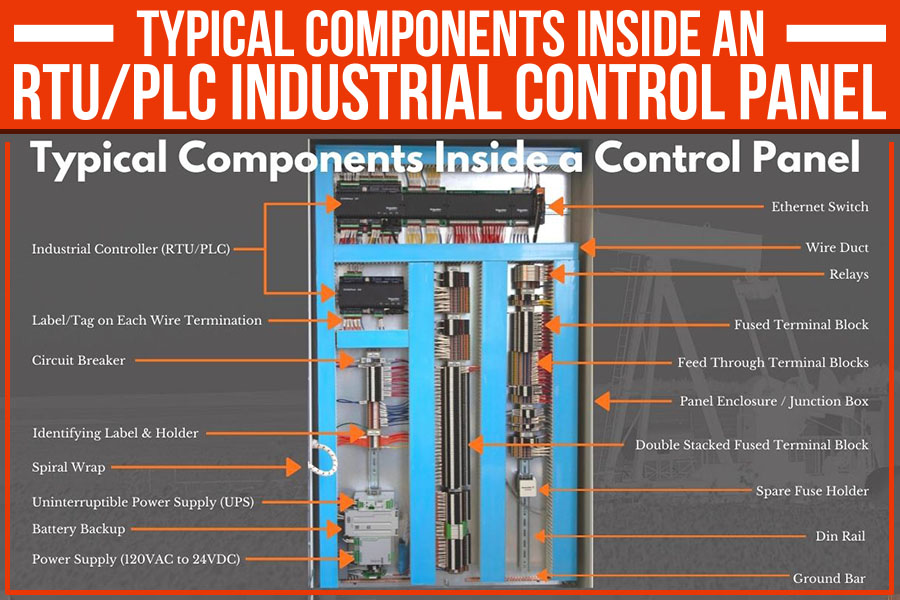
Plc Panel Components
Frequently Asked Questions (FAQs)
6. Your PLC Questions Answered
Q: What's the difference between a PLC and a microcontroller?
A: Think of a microcontroller as a single-purpose device, often embedded in a specific piece of equipment. A PLC, on the other hand, is designed for broader control applications and can be easily reprogrammed for different tasks. It's like comparing a Swiss Army knife to a single screwdriver.Q: Do I need to be a programmer to work with PLCs?
A: While programming knowledge is helpful, many PLCs use ladder logic, a graphical programming language that's relatively easy to learn. There are also many training resources available to help you get started. You don't need to be a coding ninja to get the hang of it!Q: How often do PLCs need to be replaced?
A: PLCs are built to last, and many can operate reliably for 10 years or more. However, factors like environmental conditions and usage patterns can affect their lifespan. Regular maintenance and monitoring can help extend their service life.Q: Are PLCs secure from cyberattacks?
A: Cybersecurity is a growing concern in industrial automation. It's important to implement security measures like firewalls, access controls, and regular software updates to protect PLCs from cyber threats. It's like locking the doors to your industrial control system.