Have A Info About Why Do We Use PID Controllers

Basic Principles Of PID Controllers Atelieryuwa.ciao.jp
Understanding the Ubiquity of PID Controllers
1. Why PID Controllers Reign Supreme
Ever wondered how self-driving cars manage to stay in their lane or how a sophisticated heating system keeps your home at the perfect temperature, never too hot, never too cold, just right? The unsung hero behind these marvels is often the PID controller. But what exactly is a PID controller, and why do we use PID controllers everywhere? Let's demystify this essential piece of engineering wizardry.
At its core, a PID controller is a feedback control loop mechanism used in industrial control systems and a variety of other applications requiring continuously modulated control. Think of it like a diligent thermostat, constantly monitoring the temperature and making adjustments to keep it stable. But instead of just temperature, PID controllers can manage pressure, flow rate, speed — you name it! They're the adaptable chameleons of the control world.
Now, if you are wondering what "PID" actually means, it stands for Proportional, Integral, and Derivative. These are the three musketeers of control action. Each term addresses a different aspect of the control problem, working together to achieve precise and stable control. Think of them as having different personalities: the Proportional guy reacts immediately, the Integral guy remembers the past, and the Derivative guy anticipates the future. A powerful combination, wouldn't you say?
So, why not just use a simple on/off switch? Well, that would be like trying to drive a car with only the gas pedal and the brake. You'd constantly be overshooting and undershooting your target! PID controllers provide a much smoother, more accurate way to reach and maintain a desired setpoint, preventing those annoying oscillations and ensuring that your system operates efficiently. In short, because they are good at what they are made for!

Beginners Guide PID Control The Jungle Technologia
The Three Pillars of PID Control
2. Proportional, Integral, and Derivative
Let's dive a little deeper into those three musketeers: Proportional, Integral, and Derivative control. Understanding how each component contributes to the overall control action is key to appreciating the power of PID controllers.
First, we have the Proportional term. This part provides an immediate response based on the current error — the difference between the desired setpoint and the actual value. The larger the error, the stronger the proportional response. Imagine it like this: if you're far away from your goal, you take a big step; if you're close, you take a smaller step. Simple and effective!
Next up is the Integral term. This component accounts for the history of the error. It accumulates the error over time and applies a correction to eliminate any steady-state error. Think of it as the persistent friend who reminds you of your past mistakes and gently nudges you to correct them. This is particularly useful for overcoming any persistent offsets that the proportional term might miss.
Finally, we have the Derivative term. This component anticipates future errors based on the rate of change of the current error. It acts as a dampening force, slowing down the response and preventing overshoot. This is your cautious advisor, warning you to slow down before you go too far. It's particularly useful when dealing with systems that respond very quickly.
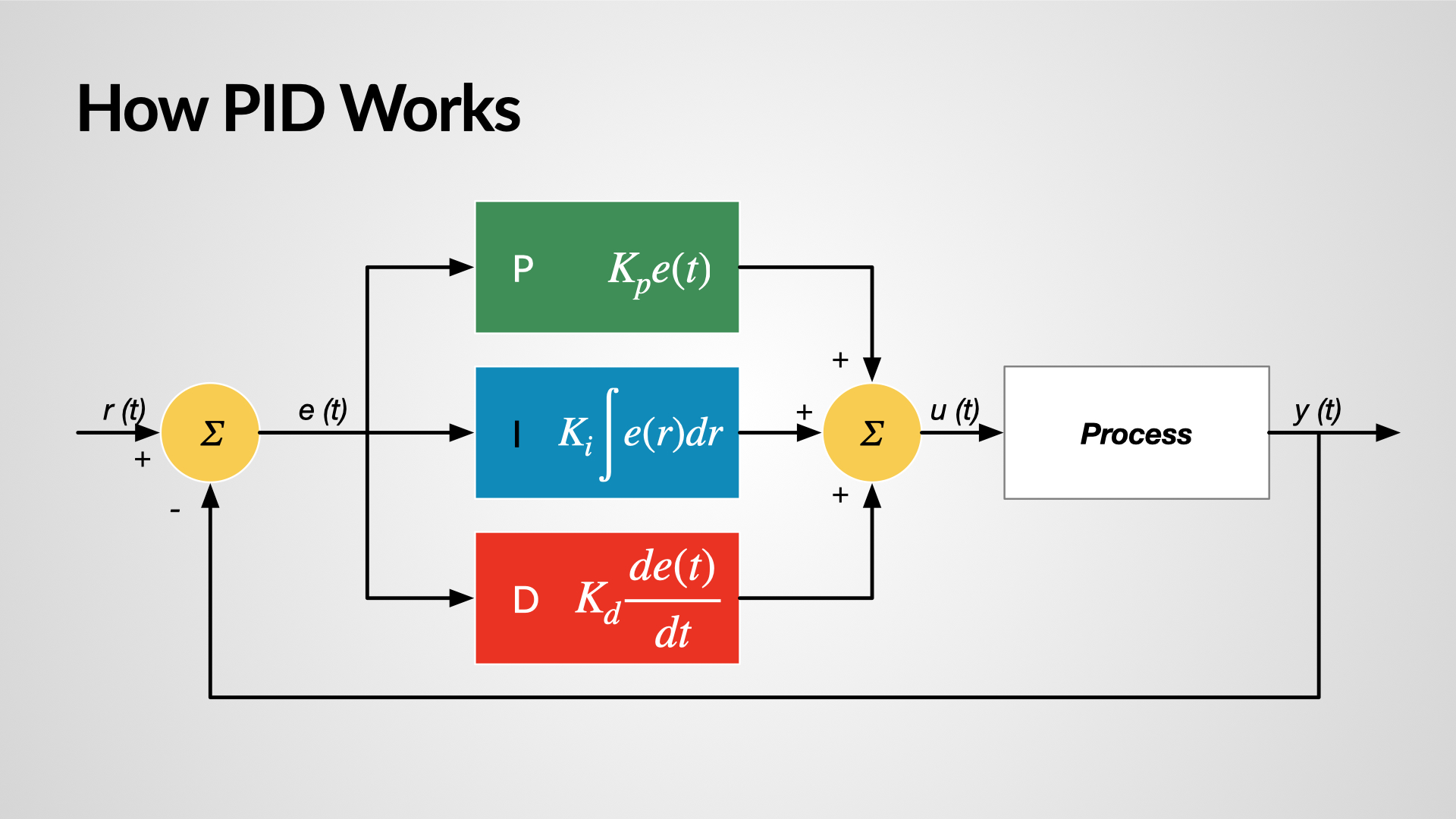
Practical Applications
3. Everywhere You Look
Now that we know what PID controllers are and how they work, let's explore some real-world applications. You'd be surprised how many devices and systems rely on PID control to function effectively.
In the realm of robotics, PID controllers are essential for precise motor control, allowing robots to perform complex tasks with accuracy and repeatability. From robotic arms welding car parts to autonomous drones navigating warehouses, PID control ensures smooth and stable movements. Without them, robots would be clumsy and unreliable.
The process control industries (chemical plants, refineries, etc.) heavily rely on PID controllers for maintaining precise temperature, pressure, and flow rates. These controllers are crucial for ensuring product quality, optimizing efficiency, and preventing potentially dangerous situations. Imagine trying to refine oil without precise temperature control! It would be a recipe for disaster.
Even your home benefits from PID control. Many modern HVAC systems use PID controllers to maintain a comfortable and consistent temperature. Instead of simply turning the heater or AC on and off, these controllers modulate the output to match your desired temperature, saving energy and improving comfort. Say goodbye to those temperature swings!
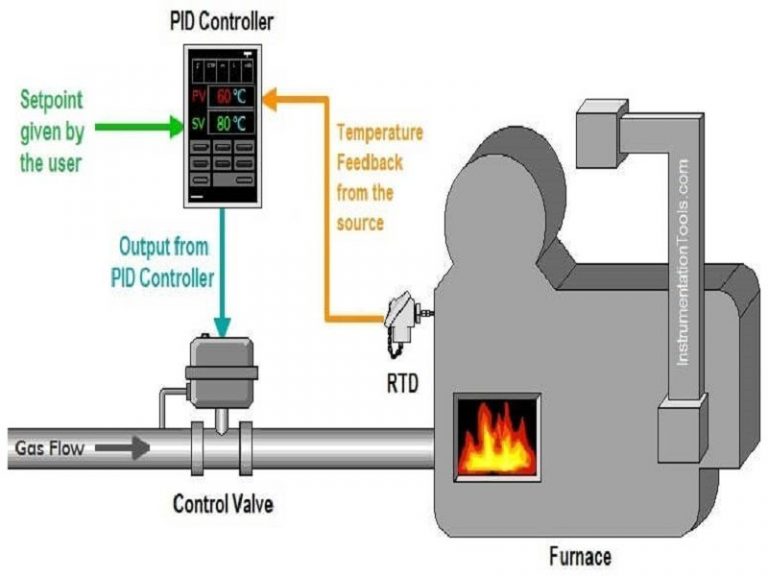
PID Controller Working & Its Applications StudiousGuy
Advantages and Disadvantages of PID Controllers
4. The Good, the Bad, and the Tunable
Like any technology, PID controllers have their strengths and weaknesses. Understanding these trade-offs is crucial for deciding when and how to use them effectively. While the reasons why do we use PID controllers are aplenty, it is not the ultimate solution.
One of the main advantages of PID controllers is their versatility. They can be applied to a wide range of control problems, from simple temperature control to complex robotic systems. They are also relatively easy to understand and implement, making them a popular choice for many engineers.
However, PID controllers can be challenging to tune effectively. Achieving optimal performance requires careful adjustment of the proportional, integral, and derivative gains. Poorly tuned PID controllers can lead to oscillations, instability, or sluggish response. Tuning often involves a mix of manual experimentation and more advanced techniques.
Another limitation of PID controllers is their performance in nonlinear systems. PID controllers are designed for linear systems, and their performance can degrade significantly when applied to highly nonlinear processes. In such cases, more advanced control techniques may be required. You'll need to assess what is the system's nature first.

Pid Controller Systems Theory Analysis Vrogue.co
The Future of PID Control
5. Beyond the Basics
While PID controllers have been around for decades, they are constantly evolving and adapting to new challenges. Advances in computing power and sensor technology are leading to more sophisticated PID control algorithms and applications.
One exciting area of development is adaptive PID control. These controllers automatically adjust their gains based on the changing characteristics of the system. This eliminates the need for manual tuning and allows the controller to maintain optimal performance even in dynamic environments.
Another trend is the integration of PID controllers with machine learning techniques. By using machine learning to learn the dynamics of the system, the PID controller can optimize its performance and adapt to unforeseen disturbances. This opens up new possibilities for intelligent control systems that can learn and improve over time.
As technology continues to advance, PID controllers will undoubtedly remain an essential tool for engineers and control system designers. Their versatility, simplicity, and effectiveness make them a timeless solution for a wide range of control problems. And despite the advances, the core principles behind them remain the same. Now, if you are thinking that it's just about the technology, think about the user, the engineer, and you'll find a lot of different aspects to improve this even more.
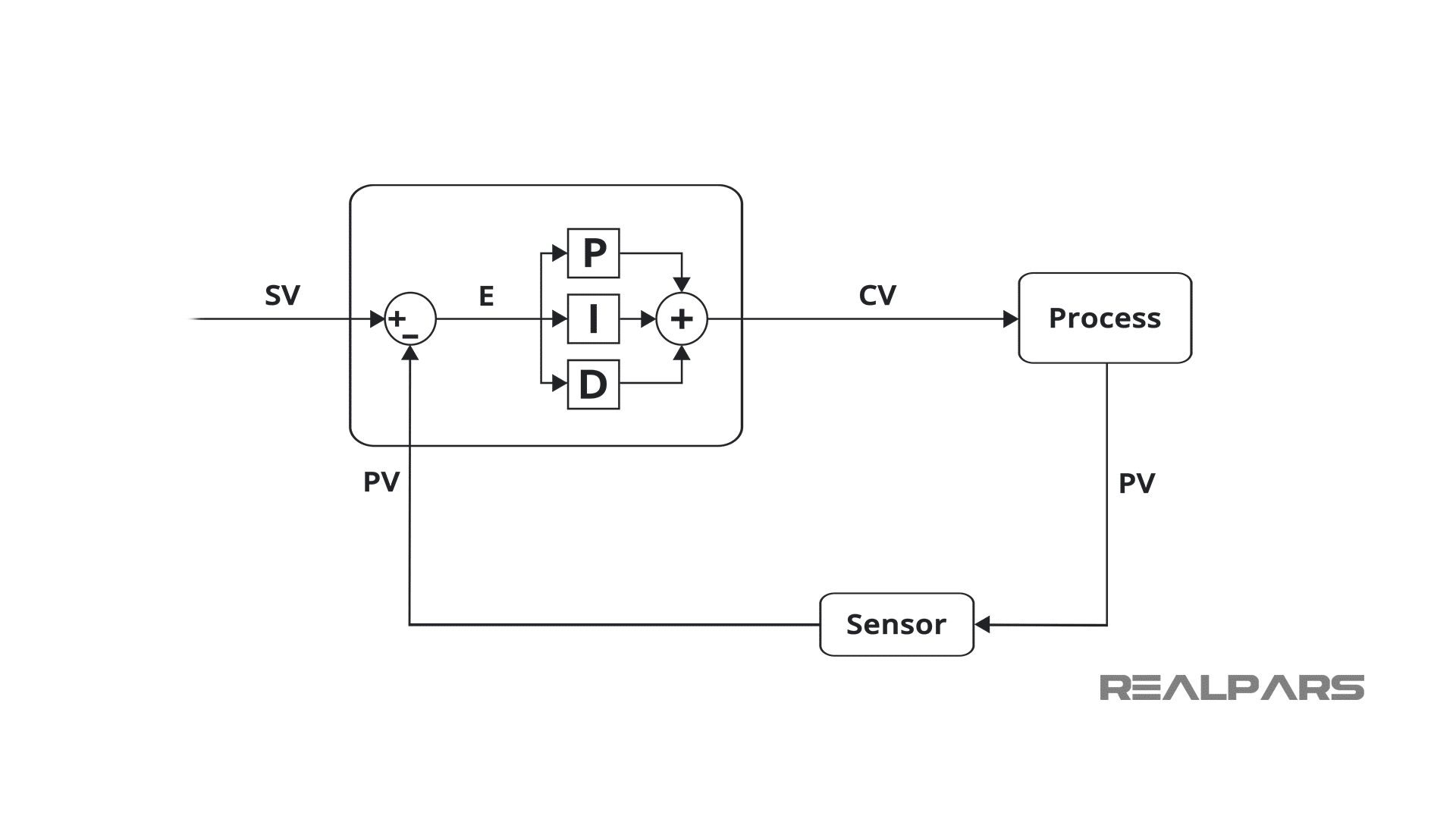
PID Tuning Explained Optimize Control Systems With RealPars
Frequently Asked Questions (FAQs)
6. What is the main advantage of using a PID controller?
The main advantage is their ability to provide stable and accurate control in a wide variety of applications. They can handle disturbances and maintain a desired setpoint effectively.
7. How do I tune a PID controller?
Tuning PID controllers can be done manually using methods like Ziegler-Nichols, or automatically using software tools that optimize the PID gains based on system response.
8. Are PID controllers suitable for all types of systems?
While versatile, PID controllers are best suited for linear systems. For highly nonlinear systems, more advanced control techniques may be necessary.