Stunning Tips About What Is The Difference Between A Pull Box And Junction
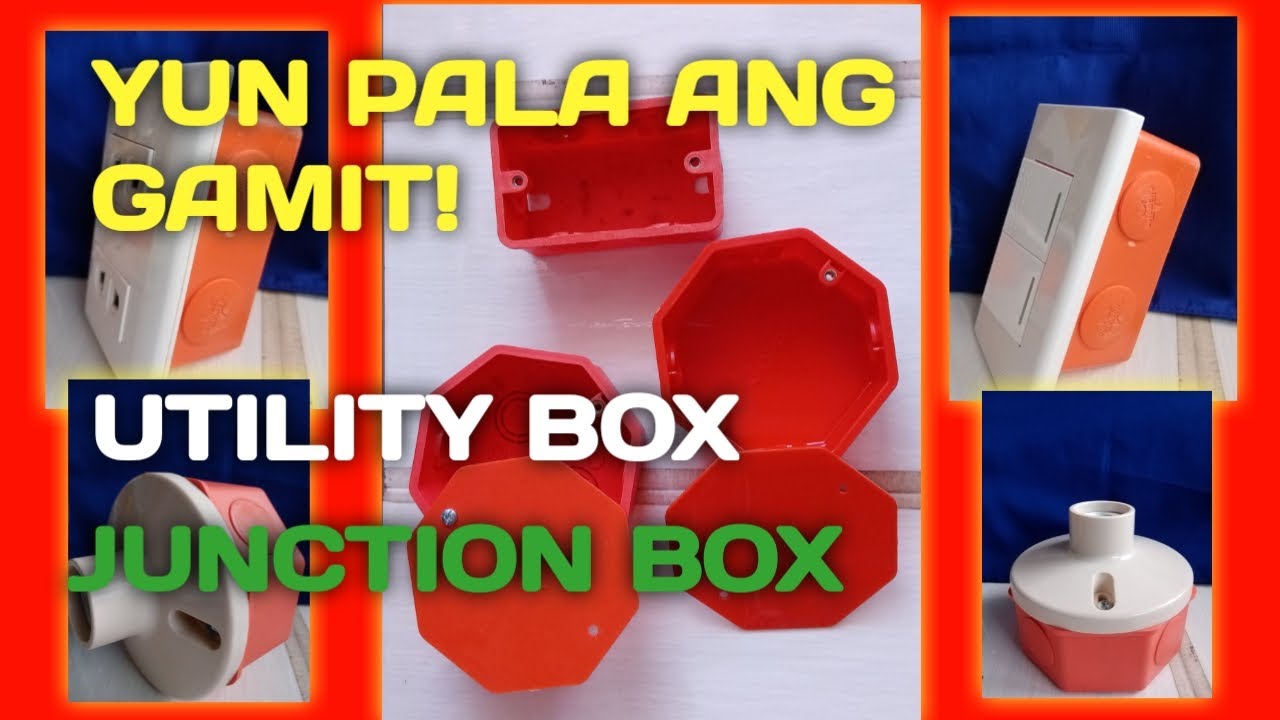
Difference Between Junction Box And Utility At Keith Barnhart Blog
Pull Box vs. Junction Box
Okay, let's untangle something that often trips up even seasoned electricians: the difference between a pull box and a junction box. At first glance, they might seem like interchangeable metal containers, but trust me, they each have a very specific role to play in the electrical world. Think of it like this: they're both boxes, sure, but one's built for a quick pit stop, and the other's more like a long-term residence for your wiring. Understanding their distinctions is key to safe and efficient electrical installations. Misusing them could lead to code violations and, more importantly, potential hazards. So, grab your metaphorical safety glasses, and let's dive in!
1. Functionality
The primary difference boils down to their intended function. A junction box, at its core, is designed to house wire splices. It's where you connect multiple wires together, extending circuits or branching them off to power different devices or appliances. It's a permanent connection point. Think of it as the central hub where electrical pathways converge and diverge. Thats where all the action happens, permanently. You secure your wires with wire connectors, ensuring a safe and reliable electrical connection.
A pull box, on the other hand, is all about making wire installations easier, especially when dealing with long runs or multiple bends. Imagine trying to thread a thick cable through a long, winding conduit. It would be a nightmare, right? That's where the pull box comes in. It's strategically placed along the conduit run to provide access for pulling the wires through. The wires pass through the box; they're not necessarily spliced or connected inside. It is really there only as a "pit stop" for the cable and nothing more!
Consider this scenario: you're wiring a large office building. You have a main electrical panel on one side and need to run power to outlets and lights on the opposite side. Rather than attempting to snake a hundred feet of cable through the conduit in one go, you'd strategically place pull boxes along the way. These boxes allow electricians to pull the cable in shorter, more manageable sections, reducing strain and preventing damage to the wires. This makes the entire process safer and much more efficient.
Essentially, one is a temporary aid, and the other is a permanent resident within the electrical system. This difference dictates their size requirements and placement, too. And yes, that will be covered later!
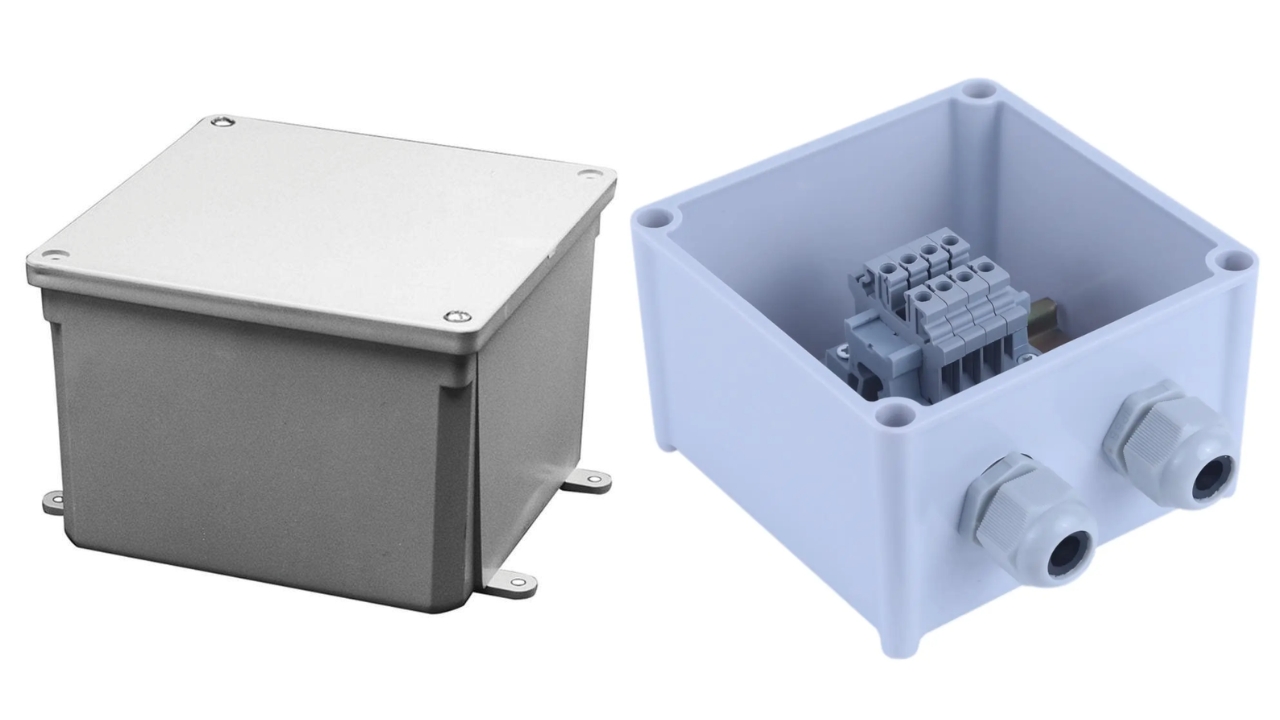
Pull Box Vs Junction Understanding The Differences, Benefits, And
Size Matters
2. Calculating the Necessary Space
When it comes to electrical boxes, size really does matter, especially in the eyes of the National Electrical Code (NEC). The NEC has specific guidelines for determining the minimum size of both junction boxes and pull boxes. These guidelines ensure theres enough space for the wires, connectors, and for heat dissipation (to prevent overheating). Ignoring these guidelines can lead to overcrowded boxes, which, in turn, can lead to insulation damage, short circuits, and even fires. It's definitely not something you want to mess with!
For junction boxes, the sizing calculation is primarily based on the number and size of the conductors entering the box. Each conductor, device (like a switch or receptacle), and fitting (like a cable clamp) has a specific volume allowance based on its size. You add up all these volume allowances, and the total must be less than or equal to the box's cubic inch capacity. Think of it like Tetris, but with wires — you need to make sure everything fits comfortably without being crammed.
Pull box sizing is a different ballgame. It's governed by the length of the conduit runs and the number of bends in the conduit. The NEC uses formulas based on these factors to determine the minimum dimensions of the pull box. The goal is to ensure there's enough space inside the box to pull the wires through without exceeding their bending radius or damaging the insulation. Imagine trying to bend a garden hose too sharply — it kinks, right? Same principle applies to electrical wires.
For example, if you have a straight pull (where the conduit enters and exits on opposite sides of the box), the pull box needs to be at least eight times the trade diameter of the largest conduit. If you have an angle pull or a U pull (where the conduit enters and exits on the same side), the calculations become more complex, involving the distance between the conduit entries and the diameter of the largest conduit. This is where knowing your NEC guidelines is an absolute must!
:max_bytes(150000):strip_icc()/electrical-switch-and-junction-boxes-1824666_02_standardrectangular-7c01a80666824af4a33ddd556abfe201.jpg)
Placement and Accessibility
3. Strategic Positioning for Optimal Function
The placement of junction boxes and pull boxes is crucial for maintaining a safe and efficient electrical system. Junction boxes, since they house permanent connections, should be located in accessible locations. This doesn't necessarily mean they need to be in plain sight, but they should be reachable without having to dismantle permanent structures. Think of attics, basements, or above suspended ceilings. The key is to ensure that an electrician can easily access them for inspection, maintenance, or repairs.
Pull boxes, as we've discussed, are strategically placed along conduit runs to facilitate wire pulling. They should be located where they provide the most benefit in reducing pulling tension and minimizing the risk of wire damage. This often means placing them at points where the conduit changes direction significantly or where the run is particularly long. Good planning here can save a lot of headaches and sore muscles during the installation process.
Consider this example: Imagine you're running conduit behind a finished wall. You definitely wouldn't want to bury a junction box there, because if a problem ever arose, you'd have to tear down the wall to access it. Instead, you'd run the conduit to an accessible location, such as an electrical panel or a fixture box, where the connections can be made safely and conveniently. It's all about thinking ahead and anticipating future maintenance needs.
Accessibility is paramount. While junction boxes can be concealed, they can't be permanently inaccessible. You cannot, for instance, bury a junction box directly in the ground without proper protection and direct burial rated enclosure. That is a big no-no! Regulations in the National Electrical Code (NEC) dictates how these boxes must be reachable.

Types Of Electrical Pull Boxes At Katie Felton Blog
Materials and Construction
4. Built to Last and Protect
Both pull boxes and junction boxes come in various materials and constructions, each suited for different environments and applications. The most common materials are steel (often galvanized or powder-coated for corrosion resistance), aluminum, and non-metallic materials like PVC. The choice of material depends on factors like the environment (indoor vs. outdoor, wet vs. dry), the type of wiring being used, and the specific requirements of the electrical code.
Steel boxes are generally used for heavy-duty applications and provide excellent mechanical protection for the wiring. They're often required in commercial and industrial settings where there's a higher risk of physical damage. Aluminum boxes offer a good balance of strength and weight and are resistant to corrosion. Non-metallic boxes, like PVC, are ideal for wet or corrosive environments, such as swimming pools or agricultural settings. They're also lightweight and easy to install.
The construction of the box also plays a critical role in its performance. Boxes must be rated for the environment in which they're installed. For example, boxes used outdoors must be weatherproof or raintight to prevent water from entering and damaging the electrical components. Some boxes are even explosion-proof, designed to contain any internal explosions and prevent them from igniting the surrounding atmosphere. These are commonly used in hazardous locations like oil refineries or chemical plants.
Think about it this way: you wouldn't use a cardboard box to protect your electrical connections in a damp basement, would you? You'd need something more robust and water-resistant, like a PVC box. Similarly, you wouldn't use a flimsy plastic box in a factory where it could be easily crushed by machinery. A steel box would be a much better choice in that situation. Matching the box to the environment is key to safety and reliability.
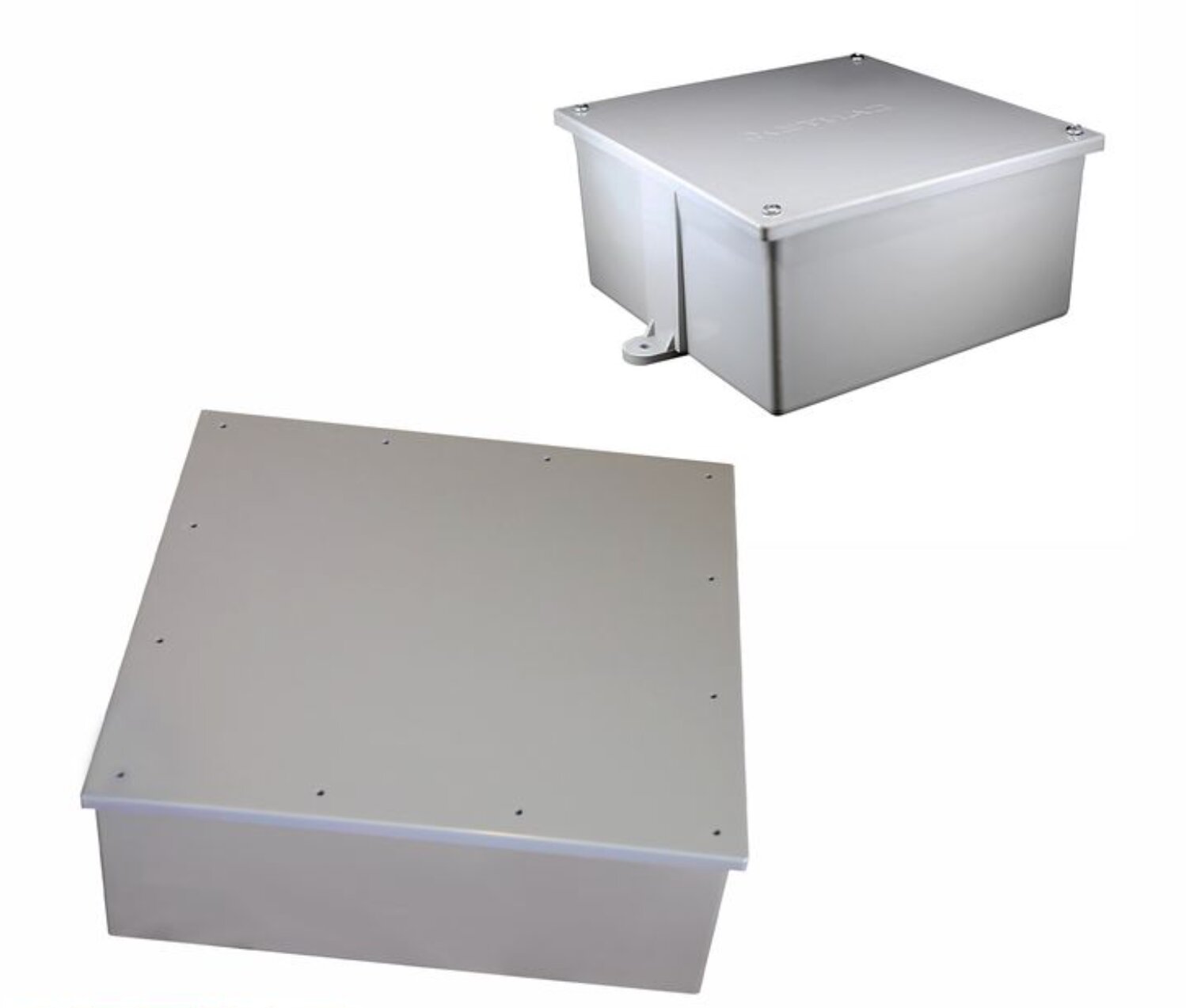
The Ultimate Guide To Welding Fixture Types, Uses, And Tips
Cost Considerations
5. Navigating the Price Range
The cost of pull boxes and junction boxes can vary significantly depending on their size, material, and construction. Generally, smaller, simpler boxes made of basic materials like steel will be the most affordable. Larger, more specialized boxes made of aluminum or non-metallic materials, or those with special features like weatherproof or explosion-proof ratings, will be more expensive. Keep in mind that the initial cost is only one part of the equation; it's also important to consider the long-term cost of maintenance and potential repairs.
When budgeting for an electrical project, it's crucial to factor in the cost of all the necessary boxes, as well as the associated labor costs for installation. It might be tempting to cut corners and use smaller or cheaper boxes to save money, but this can be a costly mistake in the long run. Using the wrong size or type of box can lead to code violations, safety hazards, and the need for expensive rework. Remember, safety and compliance should always be the top priorities.
Consider this scenario: You're rewiring your garage and decide to use smaller junction boxes to save a few dollars. However, these boxes are too small to accommodate all the wires and connectors, so you end up cramming everything in tightly. This can lead to overheating and insulation damage, potentially causing a fire. Now you're not only facing the cost of replacing the boxes but also the cost of repairing the fire damage. It's a classic case of being penny-wise and pound-foolish.
Therefore, investing in the correct boxes initially will save you money in the long run and ensure the safety and compliance of your electrical system. Always consult with a qualified electrician to determine the appropriate size and type of boxes for your specific needs. They can help you navigate the complexities of the electrical code and make informed decisions that balance budget and safety.

31428 Pull And Junction Boxes Conduit Bodies Angle
FAQ
6. Clearing Up Common Confusions
Q: Can I use a junction box as a pull box?
A: Technically, yes, you can use a junction box as a pull box if it meets the size requirements for a pull box in that specific situation. However, it's generally not recommended. Junction boxes are designed for permanent connections, and using them solely as pull points adds unnecessary complexity to the wiring. It's often better to use a dedicated pull box, which is designed specifically for that purpose.
Q: Can I splice wires inside a pull box?
A: While it's possible to splice wires inside a pull box, it's generally discouraged unless explicitly permitted by the electrical code and the box is sized appropriately for both pulling and splicing requirements. Pull boxes are primarily intended to facilitate wire pulling, and adding splices can clutter the box and make future maintenance more difficult. If you need to splice wires, it's usually best to use a dedicated junction box.
Q: What happens if I use a box that's too small?
A: Using a box that's too small can have several negative consequences. It can lead to overcrowding, which can damage the wire insulation and cause short circuits. It can also hinder heat dissipation, leading to overheating and potential fires. Moreover, it's a violation of the National Electrical Code (NEC) and can result in fines or project delays. Always ensure you're using the correct size box for the application.